Sterilization is what we do,
and we are experts at it.
Backed by the DNV Advanced Sterile Processing Certification, Instrumentum provides industry-leading off-site sterile processing, transportation of medical devices, and secure sterile storage. At Instrumentum, we invest heavily in our staff, equipment, and space to maintain our high standards.
We take pride in our clean, sterile, state-of-the-art facilities, and in providing stringently sterilized instruments EVERY TIME, allowing you to focus on more procedures and patient safety.
A Different Approach
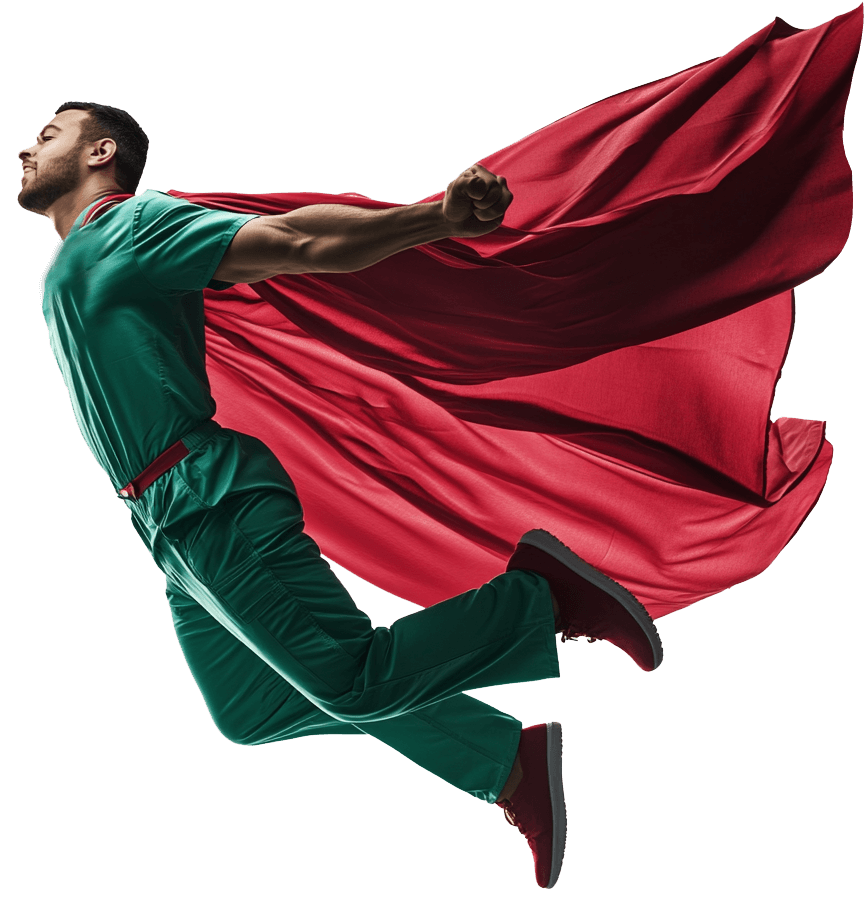
An SPD department is a cost center in a Hospital or ASC. Cost centers are constantly scrutinized to, well, lower costs. This means a lack of or out of date equipment, lower compensation, and cut corners, forcing the team to make tough choices, often at the expense of compliance and patient safety.
Not at Instrumentum. We aren’t cost cutters; we are value investors – meaning we have the best and properly maintained equipment and facilities to allow our team to do their jobs. We attract the best talent, and we pay them accordingly. We simply can’t afford to fail. EVER.
Who doesn’t benefit from that mindset?
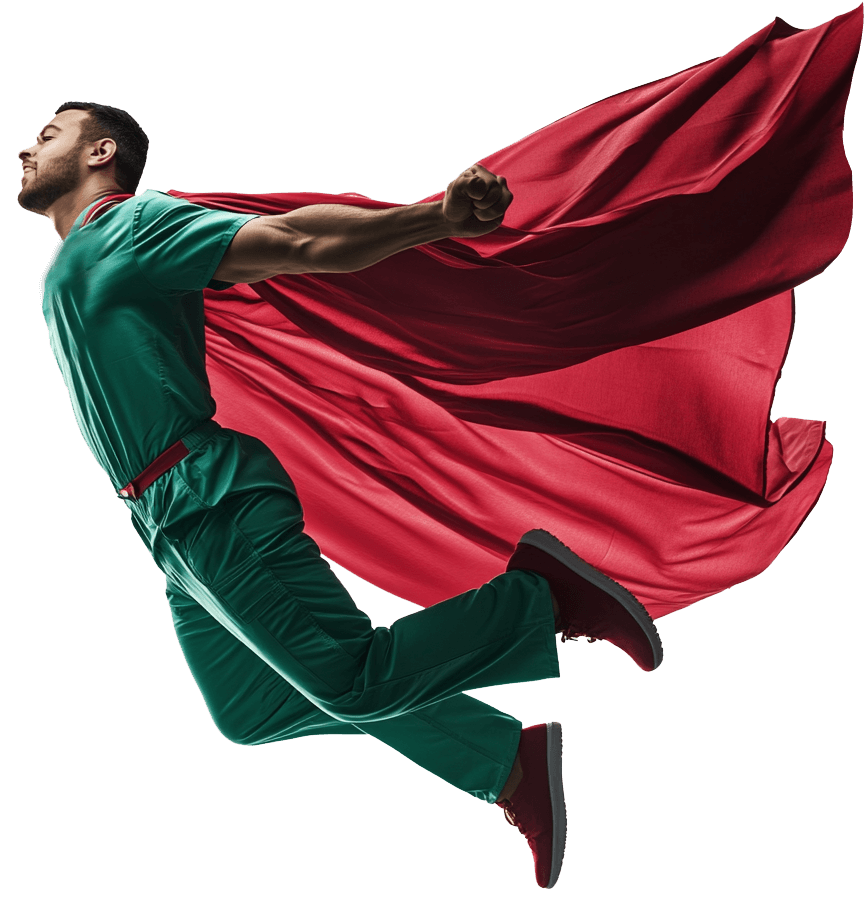
When healthcare providers partner with Instrumentum,
SPDs win.
Many SPD departments struggle with capacity and consistency.
Unlike other facilities that prioritize cost, we prevent potential issues by incorporating backup equipment and personnel into every stage of our process. This proactive approach is not just a part of our business model; it’s our commitment to ensuring uninterrupted service. Additionally, we optimize instrument turnover and utilize sterile storage, guaranteeing that trays are ready for use EVERY TIME.
Culture — The Instrumentum Way
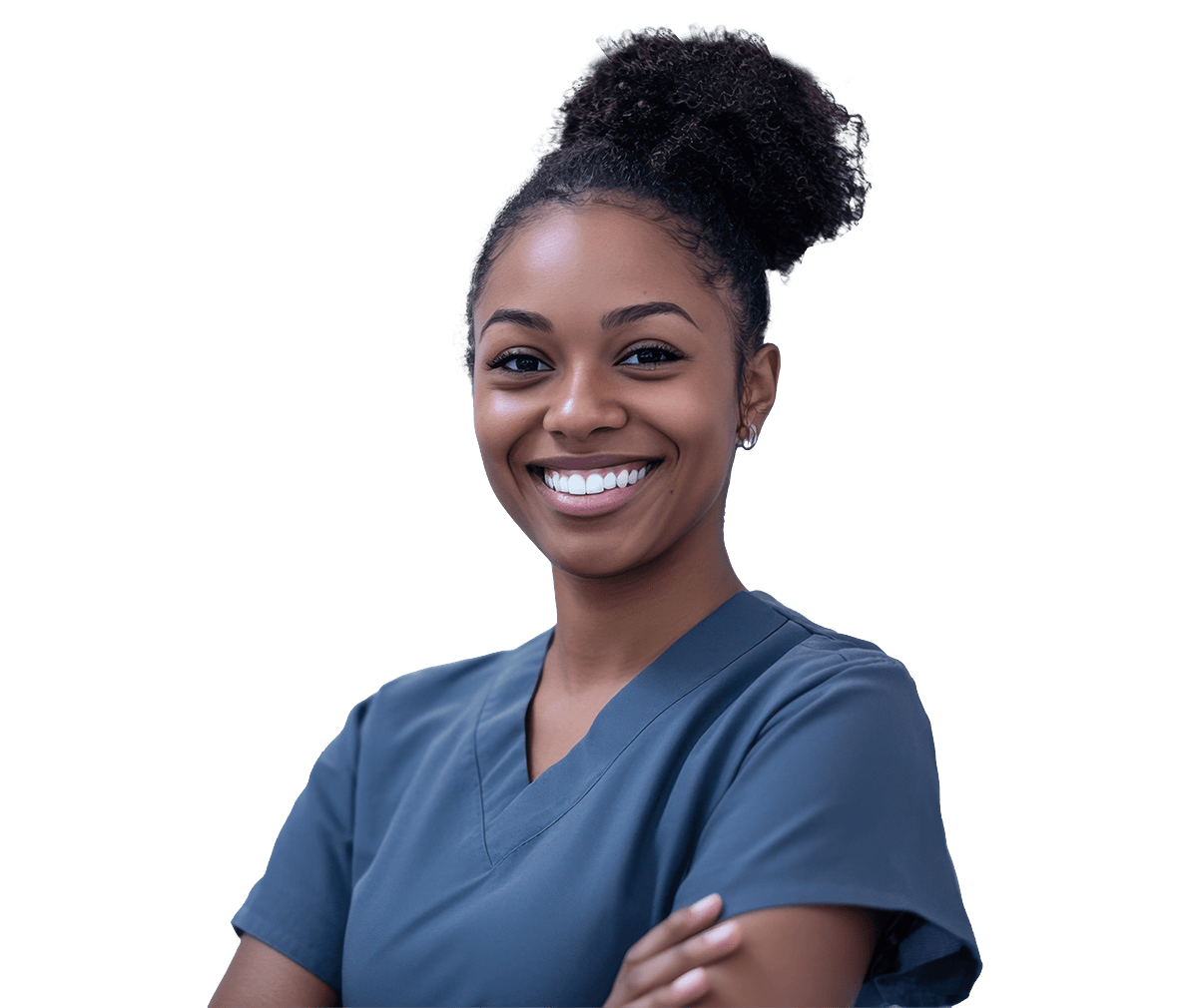
At Instrumentum, our people, equipment, and facilities are the lifeblood of our company. We invest in the right partners, and our facilities are thoughtfully designed, maintained, and regularly upgraded with expert input (including our staff) to prioritize cleanliness, organization, and natural light.
This approach attracts top talent to Instrumentum and energizes them to implement our high standards for every client EVERY TIME.
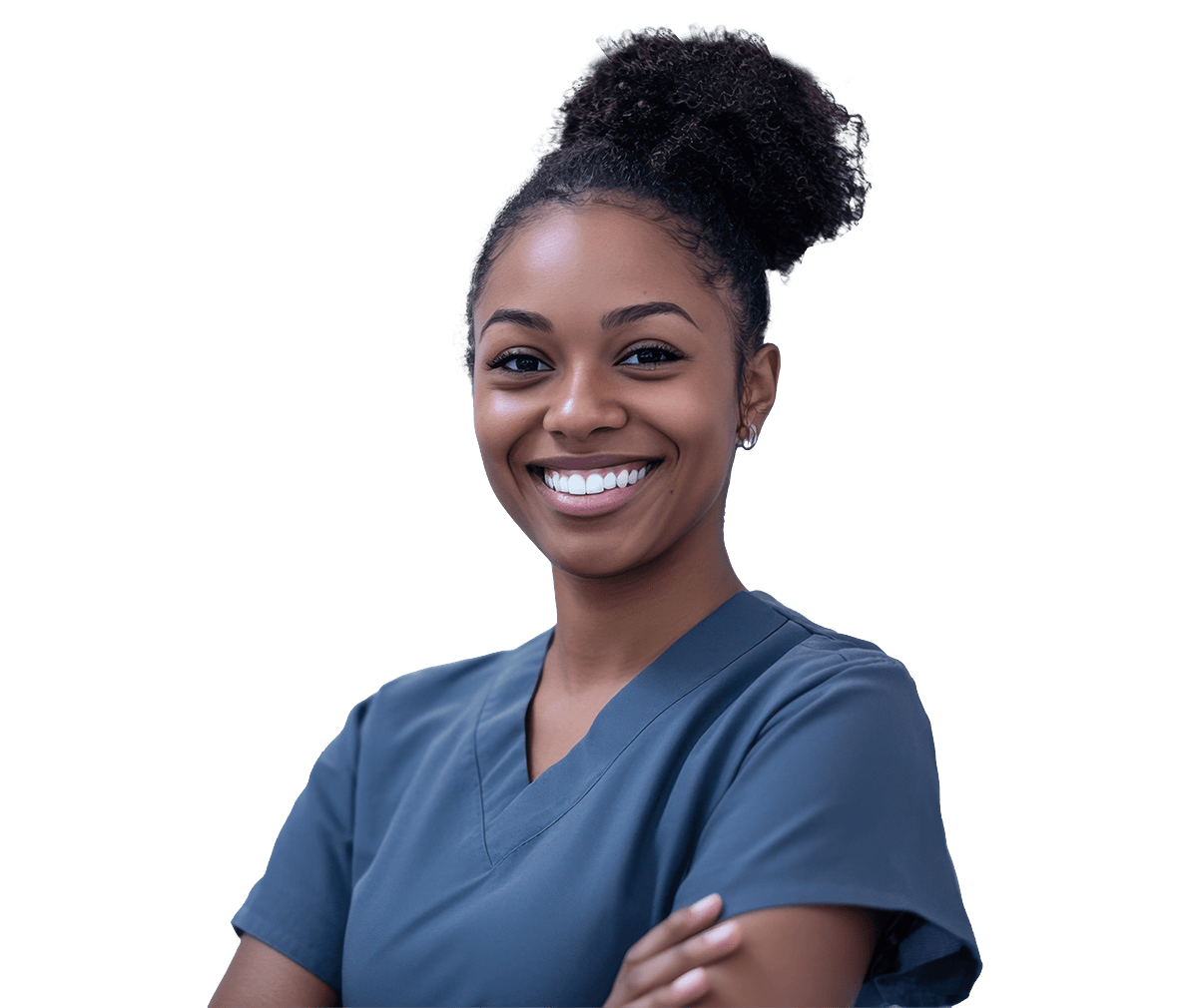